Behind the Scenes: How High-Quality Tools Are Made
- The Tool Pro
- May 4
- 3 min read
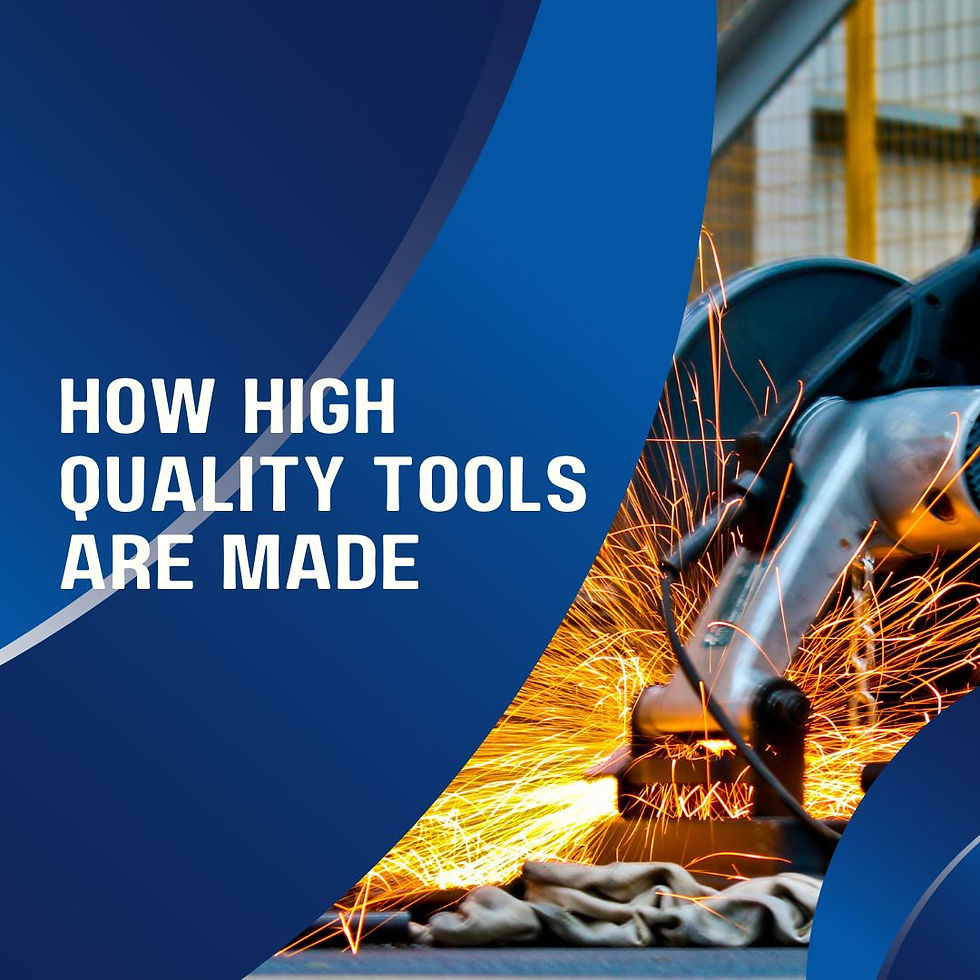
When you pick up a perfectly balanced hammer or a cordless drill that runs smoothly for years, you’re holding the result of craftsmanship, engineering, and strict quality standards. But have you ever wondered what really goes into creating high-quality tools?
Today, we’re taking you behind the scenes into the tool production process — and showing you how high-quality tools are made.
It Starts With Premium Materials
The journey to a high-quality tool begins with choosing the right raw materials.
Top manufacturers invest in:
High-grade steel for strength and durability
Chromium and vanadium alloys for corrosion resistance
Carbon fiber and composites for lightweight, heavy-duty use
Tempered plastics for ergonomic, rugged tool casings
Primary takeaway:
Premium tools materials ensure the tool can handle years of wear and tear without failing. Titanium tools are are now widley used in the home building industry and well known for their lightweight and strength. The Stilettto ClawBar is a titanium nail puller that is lightweight and a must have tool for carpenters.
Forging, Casting, and CNC Machining
How tools are made depends a lot on the manufacturing technique:
Forging: Metal is heated and hammered into shape, creating incredibly strong and durable tools like wrenches, pliers, and chisels.
Casting: Molten metal is poured into molds — good for complex shapes, though slightly less durable than forged parts.
CNC Machining: High-precision computer-controlled machines cut, drill, and grind tool parts to exact specifications. CNC machining is common for professional-grade power tools and mechanical components.
Fun Fact:
Due to their grain structure, forged tools are often 3–5 times stronger than cast versions! A great example of a quality forged tool is the BeaverCraft Bushcraft Hatchet.
Heat Treatment for Strength
After shaping, many tools undergo heat treatment to boost hardness and durability.
The process includes:
Heating the tool to high temperatures
Holding it at that temperature for a precise time
Rapidly cooling (quenching) in oil, water, or air
This makes steel tools tough enough to resist bending, breaking, and wearing down, even under heavy use.
Rigorous Testing and Quality Control
Before shipping, tool testing and quality control are critical.
Manufacturers check for:
Proper balance and weight distribution
Stress tolerance (e.g., can a wrench handle maximum torque?)
Electrical safety (for power tools)
Durability under extreme conditions (cold, heat, moisture)
Some companies even perform lifetime stress testing, simulating decades of use in just weeks.
Pro Tip:
Brands with strong reputations for quality (like Milwaukee, DeWalt, Snap-on, and Festool) put tools through dozens of tests before they hit the shelves.
Finishing Touches: Grinding, Coating, and Polishing
Before a tool reaches your hands, it gets several finishing treatments:
Precision grinding ensures perfect edges and surfaces.
Powder coatings, chrome plating, or anodizing protect against rust and corrosion.
Polishing improves both appearance and grip comfort.
Some premium hand tools even have laser-etched measurement marks, ergonomic non-slip handles, or anti-vibration features.
Bottom line:
The best tools are finished not just for looks, but for long-lasting performance.
That's How High-Quality Tools are Made
The next time you pick up a high-quality tool, remember it’s the result of expert engineering, premium materials, precision craftsmanship, and strict testing standards.
Understanding the tool production process helps explain why the best tools aren’t always the cheapest — but they are the ones that last a lifetime.
Whether forged, machined, or hand-assembled, great tools are built for excellence from the ground up.
Комментарии